December/January 2008
In this Issue
Three Decades of Housing Data
Mixed-Financing Underwrites Affordable Housing in Southwest Virginia
A Lean Makeover for Factory-Built Housing Production
Housing First for the Chronically Homeless Mentally Ill
In the next issue of ResearchWorks
A Lean Makeover for Factory-Built Housing Production
Lean production is a manufacturing approach originally developed by Toyota that strives to eradicate waste. In this case, “waste” means expenditures of time, money, materials, and other resources that do not directly contribute to producing what buyers want. The goal of lean production is to satisfy the customer by delivering the highest quality goods at the lowest cost in the shortest time.
Lean production principles are applied to both a plant’s physical characteristics and to its production processes. The former includes designing a plant layout that speeds production; improving job station design to avoid wasted time and effort on the production line; and maintaining a clean, orderly workplace. This entails adopting standardized best-practice methods; keeping inventories low; employing just-in-time order processing driven by customer demand; ensuring quick changeovers of machines; preventing defects to avoid reworking products; and other commonsense — but often overlooked — workplace goals.
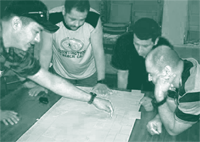
Lean production has been transforming enterprises ranging from spacecraft production to fast food, but the modular housing industry seems to have been left behind. Construction techniques typically used in HUD-code and modular homes have changed very little in the past 50 years. Does the potential exist for factory-built housing — a major contributor to the supply of affordable homes — to benefit from lean production?
A new analysis, Pilot Study: Applying Lean to Factory Home Building, is finding some answers. The study describes how nine housing manufacturing plants differing in size, location, and type of product tried lean production techniques on their own factory floors. HUD’s Office of Policy Development and Research sponsored the research through the Partnership for Advancing Technology in Housing and in conjunction with the Manufactured Housing Research Alliance.
Applying Lean Tools
In taking the first steps toward testing lean production methods, top management at each factory agreed to participate in the project. The plant then identified one or more “lean advocates” — team leaders who participated in a week of intensive training and agreed to serve as liaisons with the researchers. Together they assembled “lean teams” representing a cross-section of employees and a range of viewpoints and experiences.
The lean advocates began with a lean tool called “value stream mapping,” a sketch using boxes and arrows to illustrate each step of the production process. These diagrams capture the flow of materials and information as value is added along the production line. Lean advocates collected information such as cycle and lead time, labor requirements, inventory levels, space requirements, and quality metrics. They then worked with project researchers to identify opportunities for improvement, targeting areas with low productivity, production defects, bottlenecks, or other problems. The lean teams also drew future value stream maps to help visualize their goals.
RPIs Yield Results
With this analysis in hand, participating plants scheduled rapid process improvement (RPI) events — intensive workshops to develop and implement solutions to the targeted problems. As a result, plant production departments scored productivity improvements ranging from 10 to more than 100 percent. The report suggests that lean production techniques can provide housing plants with striking improvements in efficiency and quality. Here are two examples of RPI events drawn from the report.
-
At Hi-Tech Housing in Bristol, Indiana, value stream mapping identified a serious problem. A partition wall was taking too long to build, causing production delays. Hi-Tech minimized disruptions by holding several RPI events over the course of one to two weeks and implementing the changes on a nonproduction day.
-
The plant at Palm Harbor Homes in Albemarle, North Carolina, was small, congested, and obsolete. Damaged or excess materials and unneeded equipment were scattered throughout the plant, and necessary materials were often poorly organized. As its first lean production initiative, the plant launched a “red tag” system. A special team of managers and supervisors with the necessary decision-making authority set aside a high-visibility location marked by red flags. They asked each department to put together a list of obsolete, damaged, excess, or otherwise unneeded materials and to submit a materials return request. The lean team prioritized the list and relocated the selected materials to the “red tag” area. The team then inspected that area each Friday morning to decide whether to return these materials to the vendor, use them in another application, cut them down, scrap them, or sell them. By reselling obsolete ceramic tile and light fixtures, reshaping obsolete molding into window jambs, and other “red tag” activities, the team saved $21,282 in 6 months. Palm Harbor Homes went on to implement a second RPI in its shingle area.
Hi-Tech took the two wall-framing tables then in use and moved them under the hoist system, welding them together as one jig. Beneath the tables they added tool storage compartments with see-through steel mesh doors. Barrels of white glue, formerly located 125 feet from point of use, were placed closer to the workstations. The drywall cart was moved closer to the assembly table and mounted on ball-bearing wheels that traversed a steel track secured to the floor. The RPI team built new racks that neatly hold insulation bundles. They improved the placement of lumber racks, reducing physical strain on workers and rationalizing the flow of materials. The concrete floor was resealed, and everything was painted to foster a clean environment where it would be easier to spot problems.
Hi-Tech’s RPI event, which entailed a one-time cost of $8,000 for labor and materials, eliminated the need to add one worker to the department as orders increased, saving about $35,000 annually.
The complete report, Pilot Study: Applying Lean to Factory Home Building, is available at no cost at www.huduser.gov/publications/destech/pilotstudy.html. Readers may also be interested in an earlier report, Getting Lean: Assessing the Benefits of Lean Production in Factory Built Housing, available at www.huduser.gov/publications/manufhsg/leanprod.html.