IN THIS ISSUE:
Grantee Spotlight: University of Alaska Fairbanks Creates an Energy-Efficient Prototype Home for Harsh Winters
Wagner College Concentrates Civic Efforts in Port Richmond Community
Nancy Cantor: A Scholar in Action
Grantee Spotlight: University of Alaska Fairbanks Creates an Energy-Efficient Prototype Home
for Harsh Winters
The roof ridge connecting the corners on the northern and southern sides of the Buckland prototype home permits prevailing winds to spill over the building. Image courtesy of the Cold Climate Housing Research Center.
Bobby and Christina Snyder and their son were ready for a celebration on June 14, 2013 when they attended the open house for their new energy-efficient home in Buckland, Alaska. Also attending were representatives of the partnership that made the house possible: the University of Alaska Fairbanks, an area building science research center, and the local housing authority. With the house ready for occupancy, the partners were anticipating that its design would reduce energy use and serve as a model for affordable housing. For the Snyders, their hopes were more personal as the first winter in their new home approached — lower utility costs would ease their concerns about their household budget.
Winter in Buckland
Buckland’s winters begin in late October or early November and continue well into the spring, sometimes until May. During this long season, temperatures average between 3° and –14° Fahrenheit. Most of the homes in Buckland are heated with fuel oil. Using around 850 gallons per year at a cost of almost $10 per gallon (in 2008), the average Buckland home’s heating bill can be more than $8,000 a year — a significant expense in an area where the median household income is roughly $10,000 lower than the U.S. median household income of nearly $53,000, according to the 2007–2011 American Community Survey.
Meeting Community Needs
Leaders at the University of Alaska Fairbanks’ Chukchi Campus (UAFCC), whose mission is to inspire students to help meet the cultural and civic needs of their communities, recognized the need for more energy-efficient homes in Buckland. The Chukchi Campus, located 75 miles northwest of Buckland in the city of Kotzebue, is the smallest of the four University of Alaska Fairbanks campuses. UAFCC offers several distance learning courses, permitting students from nearby rural villages such as Buckland to complete classwork, even though no roads connect the villages with Kotzebue.
Using a HUD Alaska Native/Native Hawaiian Institutions Assisting Communities grant, UAFCC, with expertise from the Cold Climate Housing Research Center (CCHRC), developed the Snyders’ home as an energy-efficient prototype suited to the area’s severe climate. The house was constructed in Buckland as part of a Northwest Inupiat Housing Authority (NWIHA) development because NWIHA was interested in creating a prototype for efficient home construction. Construction of the house was also made possible with in-kind contributions from Buckland’s tribal council and city government. To meet the area’s need for workforce development, UAFCC also partnered with the Alaska Technical Center to train three Buckland students to help build the home.
Creating an Efficient and Context-Appropriate Home
The Buckland prototype home includes several features that make it both energy efficient and uniquely suited to Buckland’s climate. The home’s roof is designed to accommodate Buckland’s prevailing winds. The ridge of the roof runs diagonally from corner to corner, creating high corners on the northern and southern sides and low corners on the eastern and western sides. This design allows winds to spill over the home, reducing the cooling effect. A tall window installed in the high southern corner permits passive solar heating. The home’s foundation is a thermal raft, in which treated wood beams are placed on top of a gravel pad; the high R-value of this type of foundation keeps the ground under the house permanently frozen so the structure remains stable.
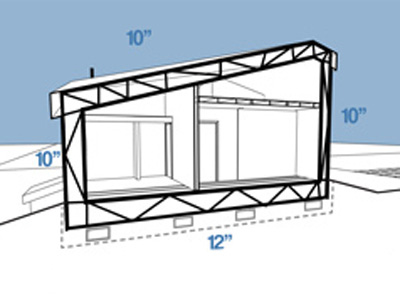
The Buckland home’s frame was quickly assembled with integrated trusses, containing the floor, wall, and roof. Image courtesy of the Cold Climate Housing Research Center.
Sitting on the foundation beams are the integrated trusses that make up the building’s frame. The trusses allow for rapid and efficient assembly — the Buckland home was completed about nine weeks after the trusses were manufactured at a plant and shipped to the site. CCHRC had previous success using integrated truss construction, with one single structural element containing walls, roof, and floor, to quickly replace flood-destroyed homes in another Alaskan village. Because of its size, the Buckland home required two separate manufactured pieces: a roof chord and an element incorporating the walls and floor, which were gusseted together to form the building frame. A soy-based polyurethane foam seals the trusses and foundation, forming a completely insulated envelope. According to Jack Hébert, president and chief executive officer of CCHRC, the foam binds the trusses together, creating a strong structure with very little thermal bridging.
Because a tight building envelope can prevent air movement and negatively affect indoor air quality, the Buckland house requires a mechanical ventilation system. To maximize efficiency, CCHRC used an integrated heating and ventilation system that filters and introduces fresh air into the building, adding heat in the process to simultaneously warm the house. Some of the heat that is added to the fresh air is recovered from existing air in the building, further improving efficiency.
According to Hébert, CCHRC’s design team, including staff members with backgrounds in anthropology, building science, and architecture, worked with the community to design the building. Hébert notes that the building reflects the lifestyle of Buckland residents, and CCHRC “add[ed] elements that ma[de] the home a high performer.” The Snyders will be collecting energy and utility data to help assess the building’s performance in its first winter. Hébert estimates that the home will use roughly 80 percent less energy for heating than a typical house in the region.
Modeling Future Home Construction
Pauline Harvey, director of the Chukchi Campus, hopes that the home will be a model for new home construction that will lower residents’ heating bills and improve their finances. Hébert says the prototype can incorporate an elevated foundation to suit a flood-prone site without significantly reducing the building’s energy efficiency. Guy Adams, executive director of NWIHA, considers the home’s construction to be a feasible alternative to conventional housing in the area, and CCHRC is helping to fine-tune more efficient home designs for the housing authority. By forging a coalition to develop the prototype home, UAFCC has built an affordable home for a local family, provided students with in-demand job skills, and possibly influenced future home construction in Buckland.